Milestone 1,2 Goals:
Milestone 1: Explore different types of actuators, and the sounds they can produce in different spaces. Determine how we can enhance these sounds in Pure Data.
Milestone 2: Make CAD models for crickets, build proof-of-concepts, and order any additional parts we might need.
Milestone 2 Progress:
The implementation of our milestone 2 goals was carried out in two separate areas. The first involved creating a box that could hold the components necessary for a cricket, and the second part was getting the Udoo to talk to a single actuator. Each of these items are described in detail below, and progress photos are also listed throughout the rest of this post.
Hardware Design of Crickets:
We decided to make a laser cut box to hold all our electronics, and to support the ‘goose-necks’ we plan to use to position and hold the actuators in place along with providing us flexibility. This box is now designed and we have a 2nd prototype of it- there are three compartments: The 1st compartment holds the Udoo, the 2nd houses the 50W x 2 Audio Amp and the 3rd holds the battery and the power/driving circuitry.
The box is strong enough to hold the weight of the goose-necks and the actuators. All sides are ‘interlocking’ except for one. This side allows service of inner electronics, as required.
The top and bottom of the box are cut with a thicker sheet of Masonite, as these would support the box or the actuators. So the plan is to allow this box to be attached to any 1/4 inch 20 bolt holder (like all tripods) so it can attach to whatever support we want. To distribute the weight, we will thread a 1/4 inch 20 into a metal sheer (similar to the template you can see in the diagram) and cut it so as to bind it to the lower side of the box. The top of the box already has space for attaching 4 actuators, as the four holed allow 4 goose-necks to be attached- we wouldn’t use more than 2 for now.
All the hardware required (screws, bolts, nuts) have been ordered.

Udoo, actuators
Our initial tests with the actuators used simple transistors connected directly to a DC power supply. This week we were able to connect a striker to the Udoo, and control it using a simple PureData software interface to the Udoo’s GPIOs.
Specifically, our striker actuator is connected to a DRV8835 dual motor driver, which uses logical power from the Udoo, and motor power from a battery back. We’ll need two of these motor drivers for each cricket, each of which will control four actuators.
The video below shows our basic setup. The next step is to make the circuitry more robust and portable, so that we can quickly scale to more actuators in week 3.
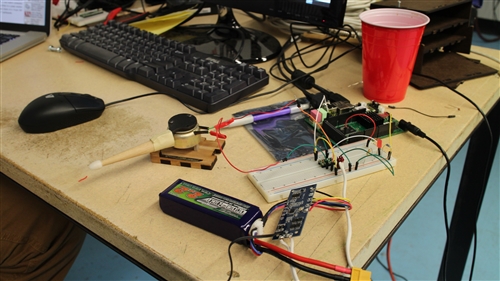